一、焊接工艺的行业困局与突破机遇
焊接与加工机器人正成为制造业升级的关键突破口。高工机器人产业研究所(GGII)数据显示,2023年焊接工艺在工业机器人应用领域占比达14.72%,稳居工艺应用前三甲。但在实际生产中,传统模式面临三大核心痛点:
1.1 传统焊接的四大挑战
- 人工依赖严重:示教模式要求±0.5mm的装卡精度,工程机械行业焊接废品率高达12%
- 柔性生产不足:固定工位设备占用15-20㎡空间,换线耗时长达4-8小时
- 质量波动明显:人工焊接产品合格率仅82%-85%,尺寸误差超标的返工成本占总成本18%
- 安全风险突出:焊接车间工伤事故率是制造业平均水平的2.3倍
2.1 模块化部署解决方案
部署方式 |
适用场景 |
空间利用率 |
转换耗时 |
固定工作台 |
标准化零件焊接 |
85% |
30min |
磁吸移动平台 |
大型钢结构件焊接 |
92% |
15min |
轨道倒装系统 |
超复杂构件焊接 |
78% |
45min |
2.2 智能焊接工艺包
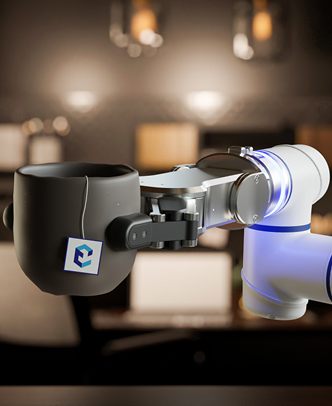
艾利特焊接与加工机器人搭载三大核心技术:
- 自适应焊缝跟踪系统:激光传感器实现±0.1mm轨迹精度
- 四维摆动算法库:支持正弦/Z字/椭圆/月牙四种摆动模式
- 工艺参数云平台:存储2000+焊接专家参数组合
三、行业应用效能实证
3.1 船舶制造案例
某造船厂引入CS625焊接与加工机器人后:
- 焊接效率提升420%(人工8小时/段 → 机器人1.9小时/段)
- 材料损耗率从15%降至3.2%
- 船体接缝超声波探伤合格率达99.3%
3.2 技术演进路线
产品研发 > 工艺优化 > 场景适配 > 效能升级
四、未来技术布局
艾利特正在构建焊接与加工机器人的三重能力矩阵:
- 扩展工作范围:CS系列已实现1800mm半径覆盖
- 提升精度等级:轨迹重复精度突破±0.03mm
- 强化场景适配:防爆型号通过GB/T 38361认证
核心数据支撑:
- 某电机厂厚板焊接项目:120mm板材焊接合格率从78%提升至99.5%
- 移动焊接工作站:场地利用率提升60%,换线时间缩短75%
- 云端工艺库:减少90%的编程调试工作量
技术对比表:
指标 |
传统工业机器人 |
艾利特协作机器人 |
提升幅度 |
部署灵活性 |
固定工位 |
全向移动 |
300% |
编程耗时 |
8小时/程序 |
0.5小时/程序 |
94% |
空间利用率 |
60%-70% |
85%-92% |
30% |
投资回收期 |
18-24个月 |
6-8个月 |
67% |
通过模块化设计、智能算法库和场景化解决方案,艾利特焊接与加工机器人正在重新定义智能制造时代的焊接标准。其技术演进路径清晰呈现:从单点突破到系统创新,最终实现焊接工艺的全面智能化变革。