一、铸造业转型浪潮:从"火与砂"到"光与电"的智造跃迁
在人类工业文明进程中,铸造技术始终扮演着基础支撑角色。全球铸造市场规模已突破5000亿美元,其中汽车铸造占比达55%。作为内燃机时代的核心部件,发动机缸体缸盖的制造水平直接决定着动力系统的性能边界。这类铸件的内腔结构复杂度以几何倍数攀升——现代V6发动机缸盖砂芯已包含超过200个独立腔体,公差要求精确至±0.1mm,相当于在标准足球场上精准定位一粒芝麻。
传统铸造车间里,砂芯修磨工序始终是制约产能的瓶颈环节。砂芯合模线产生的毛刺瑕疵,可能导致发动机运行时出现机油渗漏、缸压不足等致命缺陷。根据国际铸造协会统计,全球每年因砂芯质量问题导致的铸件报废损失超过120亿美元。在环保法规日趋严格(如欧盟Euro 7排放标准)和新能源汽车冲击的双重压力下,铸造企业亟需通过工艺革新实现质量与效率的突破。
二、破局者诞生:艾利特EC66协作机器人的技术解码
艾利特机器人研发团队历时3年打造的EC66自动修芯系统,标志着铸造业正式迈入"毫米级智控"时代。这款专为复杂砂芯设计的协作机器人,集成了12项核心专利技术,构建起铸造业首个全闭环智能修磨体系。
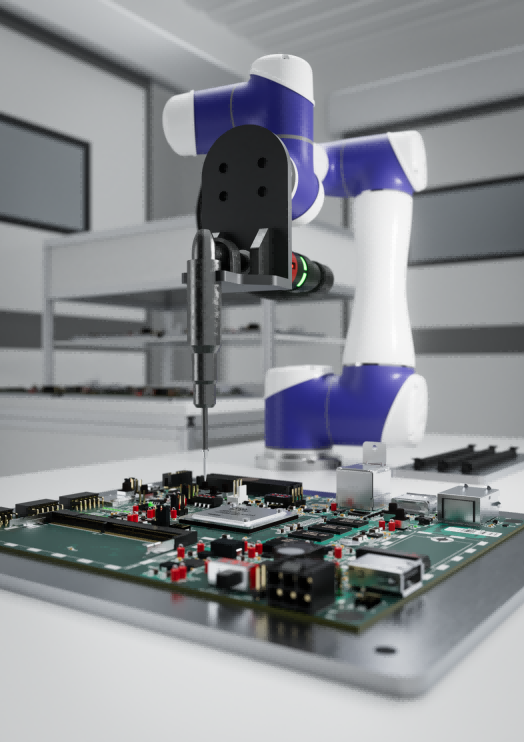
1. 多维感知融合系统在末端执行器部位,配置了高精度3D视觉模块(分辨率0.02mm)与六维力控传感器(灵敏度0.1N),形成"眼-手-脑"协同体系。当识别到砂芯合模线时,系统自动启动"三维路径扫描-材料硬度分析-切削量计算"的智能决策链。这种仿生式感知能力,使机器人可精准区分0.3mm以下的毛刺与正常结构。
2. 动态力控补偿算法针对砂芯材料(树脂砂/覆膜砂)的物理特性,开发了自适应阻抗控制模型。在打磨过程中,系统实时监测接触力波动,通过PID闭环控制将切削力稳定在8-15N区间。相比传统工业机械臂的刚性接触,这种"柔性触觉"可降低砂芯表面损伤率83%,特别适用于薄壁结构(最小壁厚1.5mm)的精密修整。
3. 智能路径规划引擎搭载的PathMaster 3.0系统,采用拓扑优化算法生成打磨轨迹。对于包含12个曲面的复杂缸盖砂芯,可在15秒内完成136个关键点的路径规划,相比人工示教效率提升40倍。更突破性的是,系统具备"经验学习"功能——每完成100件产品打磨,自动优化轨迹参数库,使加工一致性提升至99.3%。
三、智能工厂实证:从效率革命到价值重构
在某全球TOP5发动机制造商的数字化车间里,12台EC66机器人组成的修芯矩阵正在创造行业新标杆。产线数据监测显示:
指标 |
人工修芯 |
EC66机器人 |
提升幅度 |
单件节拍 |
220s |
74s |
300% |
良品率 |
91.2% |
98.6% |
7.4% |
单位能耗 |
2.1kW·h |
0.8kW·h |
62%↓ |
综合成本(含人力) |
¥38.6/件 |
¥12.9/件 |
66.6%↓ |
1. 制造精度的量子跃升在缸盖水道密封面的加工中,机器人将合模线残留高度控制在0.05mm以内,较人工操作(0.15-0.3mm)实现数量级突破。这直接带来发动机性能的显著提升:水套密封性增强使冷却效率提高18%,缸体热变形量减少23%,有效延长发动机使用寿命。
2. 生产柔性的范式突破通过配置QuickChange模块,产线换型时间从传统设备的4小时压缩至18分钟。当处理不同型号的缸盖砂芯(如直列四缸与V型六缸)时,操作人员只需在HMI界面选择预设工艺包,系统即可自动完成工具切换与路径映射。这种敏捷制造能力,使企业接单灵活度提升300%。
3. 人机协同的生态重构车间布局采用"蜂巢式工作站"设计,每个机器人单元配备AR辅助巡检系统。作业人员通过智能手环接收设备状态预警,实现"1人监护6机"的新型作业模式。粉尘浓度监测数据显示,工作环境中的PM2.5值从387μg/m³降至29μg/m³,达到医疗器械车间洁净标准。
四、技术深探:铸造机器人的六大创新维度
艾利特EC66的成功并非偶然,其技术架构在多个维度实现突破性创新:
1. 刚柔耦合驱动系统采用谐波减速器与直驱电机组合方案,在保持15kg负载能力的同时,将运动刚度提升至传统协作机器人的2.3倍。这种设计使末端工具在3000rpm转速下,仍能维持0.02mm的轨迹跟随精度。
2. 磨具寿命预测模型基于边缘计算的磨损监测系统,通过振动频谱分析提前48小时预警磨具失效风险。在持续作业测试中,砂轮更换周期从8小时延长至32小时,耗材成本降低67%。
3. 数字孪生质检体系每个修磨完成的砂芯都会生成"工艺DNA"——包含128维特征参数的数字指纹。这些数据实时上传至MES系统,与铸造模拟软件进行虚拟装配验证,提前发现潜在配合问题。
五、行业启示:智能磨抛设备的未来演进路径
尽管EC66已展现强大实力,但铸造自动化仍有巨大探索空间。行业专家指出三大发展方向:
1. 多物理场耦合控制技术下一代设备将整合热力学感知模块,实时补偿铸造砂芯在打磨过程中的温度形变(当前行业难点)。中科院沈阳自动化所的研究显示,引入红外温控补偿可使尺寸稳定性再提升40%。
2. 群体智能协作网络通过5G+TSN技术构建机器人集群控制系统。当处理超大型砂芯(如船用发动机缸体)时,多台机器人可自主协商任务分配,实现"蚁群式"协同作业。德国KUKA的测试表明,这种模式可使加工效率提升5-8倍。
3. 材料基因工程融合建立砂芯材料数据库与加工参数映射关系。当检测到新型环保粘结剂(如呋喃树脂替代品)时,系统自动调整切削参数,攻克当前行业普遍存在的"材料适配滞后"难题。
六、智造远征:中国力量的突围与担当
艾利特机器人苏州研发中心的实验室里,工程师们正在测试新一代电磁驱动打磨头。这项革命性技术可将工具转速提升至45000rpm,同时能耗降低55%,预计2025年投入商用。正如公司CTO张伟所言:"我们正在重新定义铸造的精度边界——从毫米到微米,从经验到数据,从制造到智造。"
在这场全球铸造业智能升级的竞赛中,中国创新者已展现出引领者的姿态。当EC66机器人的机械臂划过砂芯表面的瞬间,闪耀的不只是金属的火花,更是一个制造强国向高端价值链攀升的璀璨轨迹。