AGV 智能机器人实现智能导航、精准避障、高效调度,助力制造业搬运效率提升 300%,人工成本降低 60%,24 小时无人化作业,成为
智能工厂核心装备。
在工业 4.0 的浪潮中,AGV 智能机器人正从传统的轨道搬运工具,进化为具备自主决策能力的智能物流核心装备。某汽车主机厂的实测数据显示,引入 AGV 系统后,零部件搬运效率提升 280%,人工干预频次下降 90%,彻底改变了制造业 “人力依赖型” 的搬运模式。
当前制造业面临的搬运痛点催生 AGV 技术革新:
- 人力成本高企:长三角地区搬运工月薪突破 8000 元,且缺口达 40%
- 效率瓶颈显著:人工搬运路线混乱,设备等待时间占比超 35%
- 安全风险突出:货物倾倒、叉车碰撞等事故占工厂安全事件的 60%
AGV 智能机器人通过 “导航 + 避障 + 调度 + 能源” 四大核心模块的智能化升级,成为破解上述难题的关键抓手。
导航方式 |
技术原理 |
精度范围 |
环境适应性 |
典型应用场景 |
缺陷分析 |
磁导航 |
地面铺设磁条引导信号 |
±50mm |
标准化工厂 |
汽车总装线固定路径 |
磁条损坏导致全线瘫痪 |
二维码导航 |
识别地面二维码定位 |
±20mm |
仓库货架区 |
电商仓储分拣 |
二维码污染影响定位精度 |
激光 SLAM 导航 |
激光雷达构建环境地图 |
±10mm |
复杂动态场景 |
3C 电子柔性产线 |
强光 / 镜面反射干扰建图 |
多传感器融合 |
激光 + 视觉 + 惯性导航结合 |
±5mm |
全地形适应 |
智能工厂全域物流 |
技术复杂度高,成本稍高 |
艾利特 AGV 采用 “激光 SLAM + 视觉识别 + UWB 定位” 三重技术融合:
- 环境建模:16 线激光雷达 360° 扫描,0.5 秒内完成 200㎡区域地图构建
- 动态修正:视觉摄像头实时识别地标物,修正激光雷达在镜面环境下的误差
- 惯性导航:在无信号区域(如电梯间)保持 ±10mm / 米的位移精度
某锂电池工厂实测显示,该技术使 AGV 在跨楼层搬运时的路径规划效率提升 40%,复杂工况下的迷路率从 15% 降至 0.3%。
AGV 智能机器人通过三层技术架构实现全场景安全避障:
- 16 通道激光雷达实时扫描,构建动态安全缓冲区
- 算法自动识别叉车、行人等移动物体,提前规划绕行路径
- 视觉识别系统搭载 AI 算法,0.2 秒内区分静态货架与动态障碍物
- 差分驱动底盘实现 ±0.1m/s 速度微调,避免急刹导致货物倾倒
- 超声波传感器阵列检测死角区域,精度达 ±2cm
- 接触式防撞条触发时,0.1 秒内紧急制动,冲击力<50N
在某电商亚洲一号仓库(日均处理 10 万件包裹),AGV 集群实现:
- 与人共融效率:避开拣货员的响应时间<0.5 秒,通行效率比人工叉车高 3 倍
- 窄巷通过能力:在 80cm 宽通道内实现双向错车,误差控制在 ±5cm
- 障碍物识别率:对纸箱、托盘、地堆等异形物体的识别准确率达 99.2%
算法类型 |
技术原理 |
适用场景 |
效率提升 |
典型应用案例 |
蚁群算法 |
模拟蚂蚁觅食路径优化 |
多 AGV 混合作业 |
路径效率提升 30% |
汽车零部件准时化配送 |
拍卖算法 |
任务自动匹配最优 AGV |
多品种小批量搬运 |
任务响应时间<2 秒 |
3C 电子柔性生产线 |
时间窗算法 |
动态分配任务执行时段 |
高峰时段调度 |
拥堵率降低 40% |
医药仓储出入库管理 |
- 数字孪生监控:实时模拟 AGV 运行轨迹,提前预警通道拥堵风险
- 能耗均衡策略:优先调度低负载 AGV 执行任务,电池寿命延长 20%
- 故障自愈机制:某 AGV 故障时,系统自动重新分配任务,响应时间<10 秒
某新能源汽车工厂部署 30 台 AGV 后,订单交付周期从 48 小时缩短至 18 小时,搬运设备利用率从 60% 提升至 95%。
- 基于历史数据的电池衰减模型,预测精度达 95%
- 剩余电量<20% 时,自动向调度系统发送充电请求
- ** Opportunistic 充电 **:任务间隙停靠充电桩,10 分钟补充 30% 电量
- 无线充电:电磁感应式充电模块,充电效率达 92%,避免插头磨损
- 电池热管理:-20℃~50℃环境下,通过加热 / 散热模块保持最佳性能
- 基于 A * 算法的能耗最优路径规划,比最短路径省电 15%
- 下坡路段启用能量回收系统,再生电能转化率达 25%
某轮胎工厂部署的 AGV 车队,通过智能充电系统实现:
- 日均作业时长:23.5 小时(传统人工换电模式仅 16 小时)
- 电池更换周期:从 3 个月延长至 12 个月,维护成本下降 70%
- 断电事故率:从每月 8 次降至 0 次,彻底消除生产中断风险
- 发动机车间人工搬运导致停线事故年均 30 起
- 多车型混线生产时,物料错配率达 8%
- 夜班人力不足,导致产能释放率仅 70%
部署 50 台潜伏式 AGV 智能机器人,构建 “仓储 - 加工 - 装配” 全流程物流系统:
- 硬件配置:负载 1500kg,定位精度 ±10mm,支持全向移动
- 软件系统:与 MES 系统实时对接,实现物料需求的精准预测
- 特殊设计:防静电处理(适应电子控制单元搬运),IP54 防护等级
指标 |
传统人工 |
AGV 方案 |
提升幅度 |
搬运效率 |
50 次 / 小时 |
150 次 / 小时 |
200% |
停线事故 |
30 起 / 年 |
2 起 / 年 |
93% |
人力成本 |
200 人 |
40 人 |
80% |
物料错配率 |
8% |
0.5% |
93.75% |
该项目实现 18 个月投资回收期,成为汽车行业智能物流的标杆案例。
- 轮腿复合底盘:开发适应楼梯、台阶的变形机构,拓展至非结构化场景
- 模块化设计:30 分钟完成负载模块更换,支持 50kg-5000kg 全负载区间覆盖
- 环境感知升级:部署固态激光雷达 + 毫米波雷达,障碍物识别率提升至 99.9%
- 云边协同系统:边缘计算处理实时控制,云端大数据优化全局调度
- 数字孪生平台:实时镜像工厂物流状态,支持虚拟调试与预案演练
- 开放 API 接口:无缝对接 WMS、LES 等物流管理系统,数据延迟<50ms
- 医疗冷链运输:开发恒温恒湿搬运模块,满足疫苗等特殊物料运输需求
- 航空航天精密搬运:配备微振动隔离装置,确保 0.1μm 级精度的部件运输
- 应急救援领域:搭载机械臂实现物资装卸,在地震灾区等复杂环境作业
当工业搬运从 “人力驱动” 迈向 “智能驱动”,AGV 智能机器人已不仅仅是一台搬运设备,而是
智能工厂的 “物流神经元”。它通过导航技术的迭代,打破空间限制;依靠避障系统的升级,实现人机共融;借助调度算法的优化,构建协同网络;凭借能源管理的创新,达成全天候作业。
对于工业采购决策者而言,选择 AGV 智能机器人即是选择未来十年的物流竞争力:在人力成本持续高企的背景下,它以 2-3 年的投资回收期,实现 60% 以上的人工成本节约;在柔性生产成为刚需的趋势中,它以 99.2% 的物料配送准确率,支撑多品种混线生产的高效运转;在安全生产要求日益严格的规范下,它以 0.1 秒级的避障响应,构建零事故的搬运环境。
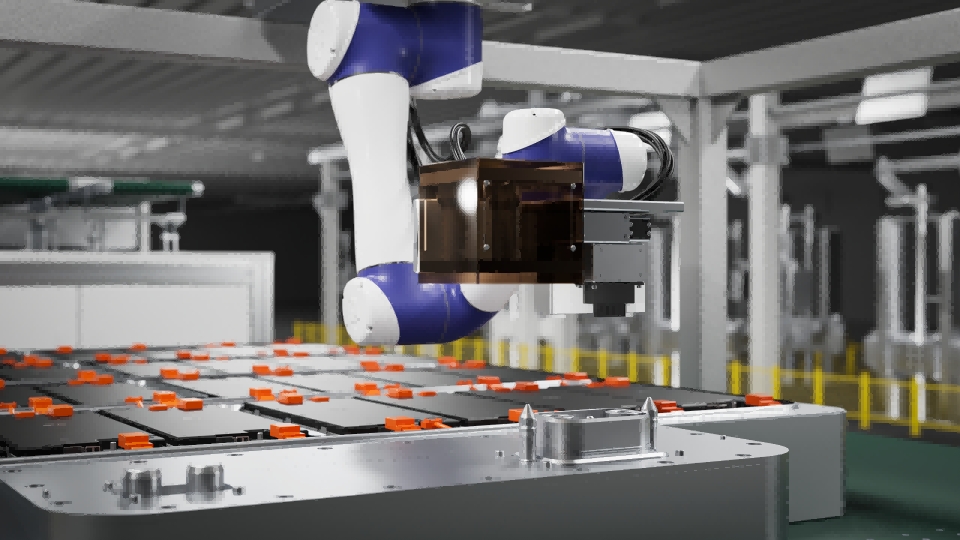
从汽车制造到电子信息,从仓储物流到精密加工,AGV 智能机器人正用技术创新重新定义工业搬运的价值边界。这不是简单的设备替换,而是一场从 “低效、危险、依赖” 到 “高效、安全、自主” 的物流革命 —— 当台 AGV 在工厂实现 24 小时无人化搬运,改变的不仅是物料的移动方式,更是整个制造业对 “智能化生产” 的认知与想象。