引言:柔性制造时代下的3C产业变革机遇
在工业4.0浪潮席卷全球的背景下,柔性制造系统(FMS)正以年均15%的增速重构制造业格局。作为全球电子产品制造核心基地,中国3C电子行业面临个性化定制需求激增与人力成本上升的双重挑战,这倒逼企业加速向智能化、柔性化生产转型。艾利特机器人凭借自主研发的3C机器人解决方案,在激光切割、质量检测、精密装配等关键环节实现突破性应用,为行业打造可复制的智能制造标杆。
核心优势解析:3C机器人技术矩阵与价值创造
1. 全场景覆盖的协作机器人产品体系
艾利特构建起完善的3C机器人技术矩阵,形成三大核心产品系列:
- E10系列(10kg负载):专为精密加工设计,配备第七轴导轨实现多工位联动
- Elfin系列(3-5kg负载):紧凑型设计适配狭窄空间作业,±360°关节活动范围突破空间限制
- E05系列(5kg负载):高防护等级(IP66)应对恶劣工况,±0.02mm重复定位精度保障工艺稳定性
2. 柔性制造四大技术突破点
|
graph LR |
|
A[智能路径规划] --> B(振动抑制算法) |
|
B --> C[自适应力控系统] |
|
C --> D[模块化快换装置] |
|
D --> E[视觉引导定位] |
- 振动抑制技术:E10-L机型涂胶轨迹精度达0.05mm,较人工操作效率提升40%
- 快速部署系统:Elfin系列实现2小时快速换线,产线停机时间缩短80%
- 人机协作安全:通过ISO/TS 15066认证,碰撞检测响应时间<0.1秒
- 数字孪生支持:内置仿真软件降低调试成本30%以上
行业应用图谱:六大典型场景深度实践
场景一:精密加工自动化(手机屏激光切割)
应用案例:深圳某激光加工企业
- 技术方案:1台E10协作机器人服务4台切割设备,第七轴导轨实现X/Y/Z三向移动
- 效能提升:
- 单班人力需求从4人减至1人
- 设备利用率从65%提升至92%
- 入选《深圳市智能机器人应用示范典型案例》
- 客户证言:"系统上线后产品良率提升至99.7%,较传统方式节省32%能耗"
场景二:质量检测智能化(智能手机瑕疵分拣)
应用数据:全球Top3手机品牌代工厂实证
- 检测指标:
- 识别精度:0.01mm²微小缺陷
- 检测速度:1.2秒/件(人工需5-8秒)
- 误判率:从3.2%降至0.08%
- 部署优势:▶️ 无需改造现有产线布局▶️ 72小时完成方案导入▶️ ROI周期缩短至8个月
场景三:PCB板处理无人化
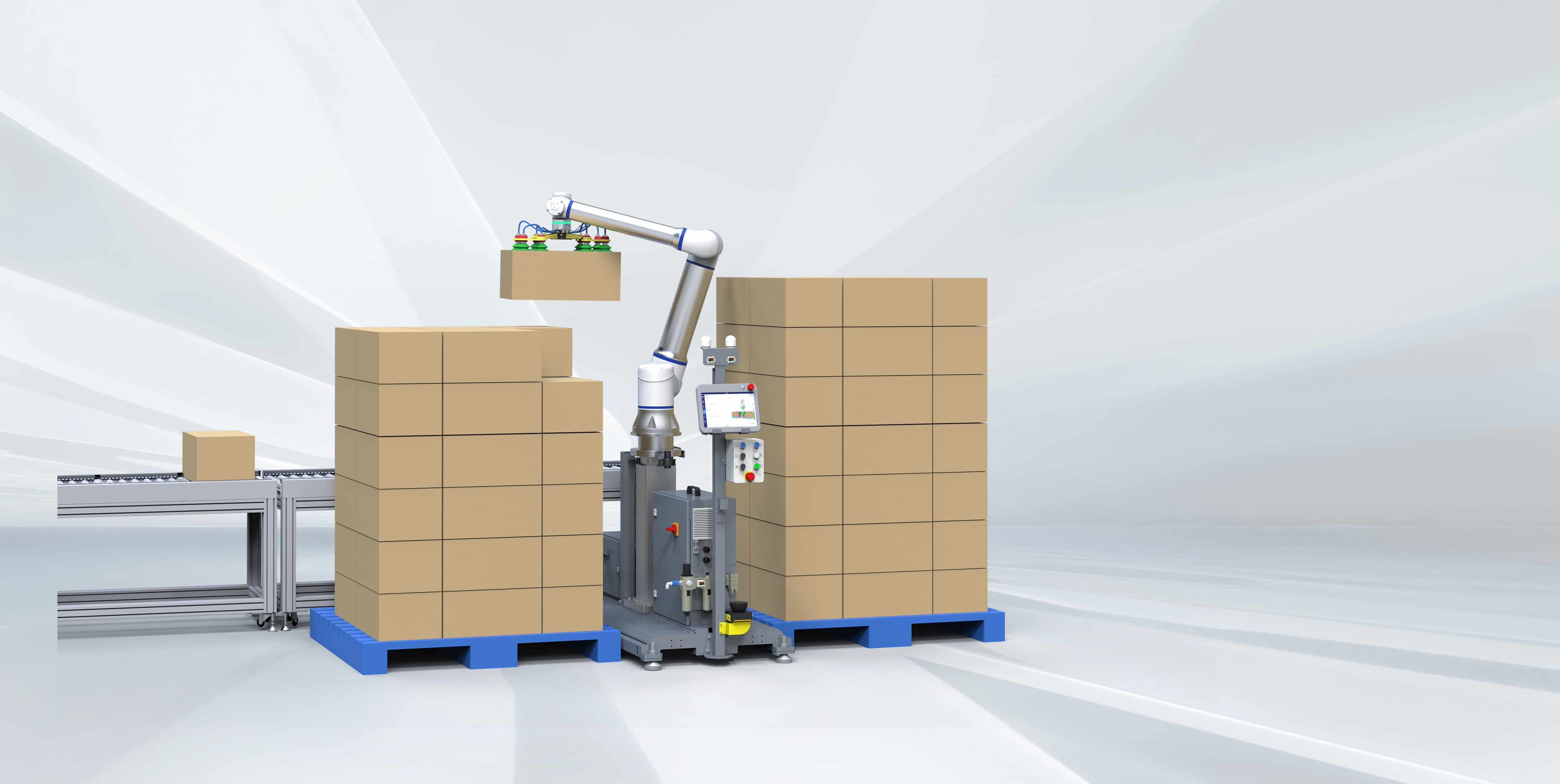
工艺流程优化:
- 铜箔抓取:真空吸盘实现0.2N柔性抓取
- 隔板放置:自动识别防擦花膜层
- 装箱作业:符合IPC-A-610E三级标准
- 效益对比:
指标 |
人工操作 |
机器人作业 |
改善率 |
破损率 |
2.1% |
0.05% |
-97.6% |
单位能耗 |
0.18kWh |
0.06kWh |
-66.7% |
作业空间 |
4.5㎡ |
1.2㎡ |
-73.3% |
典型客户案例:电子元器件制造升级路径
案例一:某军工企业热敏电阻产线改造
痛点分析:
- 高温托盘更换作业存在安全风险
- 化学药剂暴露影响员工健康
- 传统机械臂改造周期长达6个月
解决方案:
- 部署E05协作机器人执行高温工位操作
- 配置IP66防护等级应对腐蚀环境
- 集成MES系统实现生产数据追溯
实施效果:✅ 工伤事故率归零✅ 产能提升2.3倍✅ 年维护成本降低58%
案例二:电源适配器产线人机协作创新
协同模式:
- 建立安全隔离工作舱(符合ISO 10218-1)
- 机器人负责螺丝锁付(扭矩精度±5%)
- 人工进行外观终检
- 实现24小时连续生产
价值创造:
- 单位人时产出从120件提升至380件
- 锁付不良率从1.8%降至0.03%
- 员工流失率下降65%
实施方法论:四步走转型路径
- 需求诊断阶段
- 通过3D扫描建立产线数字孪生
- 运用OEE分析定位瓶颈工序
- 制定ROI预测模型(精度达±8%)
- 方案设计阶段
- 开发仿真验证平台
- 设计模块化工艺包(含20+标准工艺模板)
- 制定安全风险评估报告(符合ISO 12100)
- 部署实施阶段
- 采用预组装导轨系统(安装时间缩短70%)
- 实施AGV物料对接方案
- 配置云端运维管理系统
- 运营优化阶段
- 部署AI视觉检测模块
- 建立预测性维护模型
- 开发技能培训数字孪生系统
未来展望:3C机器人技术演进方向
- 复合机器人系统:集成AGV与机械臂实现物料流转全自动化
- AI赋能升级:通过边缘计算实现工艺参数自优化
- 数字孪生深化:构建产线级虚拟调试环境
- 生态协同创新:与MES/ERP系统深度集成