一、3C产业升级的「智造之困」与破局关键
在智能手机年产超13亿台、TWS耳机全球市场规模突破千亿的产业背景下,3C制造正面临三重核心挑战:
- 工艺精度要求指数级提升
- 智能穿戴设备装配公差进入$ \pm0.05mm $时代
- 微型马达组装需克服$ 1.5N \cdot m $精准力矩控制
- 产线换型周期压缩67%
- 某头部手机品牌产线切换频率达15次/月
- 新机型导入周期从72小时缩短至24小时
- 人机协作安全标准升级
- ISO/TS 15066规定协作单元风险值须低于$ 150N/mm^2 $
传统解决方案痛点 |
艾利特破局路径 |
专机改造周期>45天 |
即插即用部署<72小时 |
单工位综合成本>¥28万 |
ROI回收周期<8个月 |
人机隔离导致柔性缺失 |
动态避障响应<0.3s |
二、EC系列协作机器人的「技术解码」
(一)基础能力矩阵
class ECobot_Core:
def __init__(self):
self.repeatability = "±0.02mm" # 重复定位精度
self.payload = "12kg" # 有效负载
self.safety = {
"force_limit": "130N",
"collision_detect": "0.1ms响应"
}
self.interface = ["EtherCAT", "PROFINET", "Modbus-TCP"]
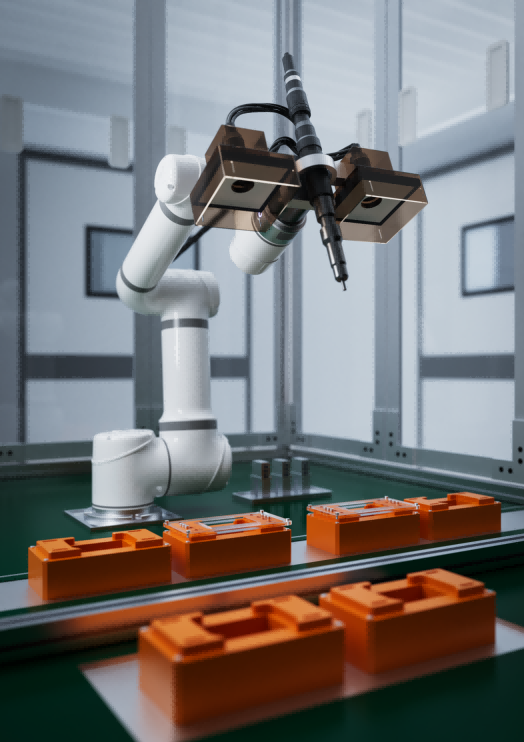
(二)场景化技术进化树
-
精密装配模组
- 六维力控传感器实现$ F_z= \pm3N $精准接触力感知
- 视觉引导系统达成$ \mu m $级元件对位
-
动态换型系统
- 基于数字孪生的工艺包切换<15分钟
- 末端快换装置支持12种工具自动识别
-
人机协同中枢
- 3D安全场实时计算$ \sqrt{(x^2 + y^2 + z^2)} $风险值
- 动态功率限制算法确保接触能量<6J
三、从单点突破到生态重构的「价值跃迁」
(一)某全球TOP3手机厂商实践样本
项目背景
- 产品线:折叠屏手机转轴组装
- 核心痛点:人工良率波动(62%-78%),产能天花板明显
实施路径
- 部署12台EC612协作机器人
- 集成高精度力矩传感器(分辨率$ 0.01N \cdot m $)
- 配置视觉纠偏系统(定位精度$ 0.015mm $)
价值产出
- 装配节拍从23秒提升至15秒(提升35%)
- 产品良率稳定在98.7%水平
- 产线改造成本降低40%(对比传统自动化方案)
(二)产业级价值传导模型
$$ \begin{cases} \text{设备层} & \rightarrow \text{单线产能提升30%-50%} \ \text{工厂层} & \rightarrow \text{空间利用率提升200%} \ \text{生态层} & \rightarrow \text{新产品导入周期缩短60%} \end{cases} $$
四、致3C智造决策者的「进化倡议」
-
构建柔性化能力基线
- 2025年前实现关键工位100%可重构
- 建立工艺参数数字资产库(建议存储≥500组工艺包)
-
设计人机协同新范式
- 采用「3+3」布局原则:3米内3种人机交互模式
- 实施动态风险评估(建议频率:1次/15分钟)
-
把握技术进化窗口期
- 关注协作机器人负载精度曲线(当前年均提升18%)
- 跟踪智能算法迭代周期(当前每6个月突破关键指标)